В России при приобретении подвижного состава главными действующими лицами по-прежнему выступают представители автопроизводителей. Даже крупные перевозчики часто обращаются к ним для формирования всего автопоезда. Причины бывают разными. В истории, о которой пойдет речь, основанием было выгодное финансирование на весь автопоезд.
Отдел продаж европейского автопроизводителя выходит с предложением продать партию автопоездов через его финансовую структуру для VIP-клиента – известной транспортной компании. У перевозчика возникло желание приобрести полуприцепы австрийской фирмы Schwarzmüller. К моему удивлению, автопроизводитель обозначил свой интерес только в увеличении объема денежной массы их финансового подразделения. Дилерская комиссия за продажу прицепов была нулевая. Да, так иногда бывает. Получив контакты перевозчика, мы стали общаться напрямую.
Механик — главное исполнительное лицо работы автопарка
Любой проект с производителем прицепов начинается с технических требований. Обычно их формирует и отправляет механик. Независимо от размера автопредприятия, типа его бизнес-модели и должности, занимаемой механиком, эффективность работы механика является показателем исполнения задуманных планов.
Осуществление желаний и мечтаний логистов, работа с водителями, вопросы эксплуатации и ремонта подвижного состава замыкаются на механика или возглавляемое им подразделение. Находясь под постоянным давлением, с одной стороны, руководства и логистов, с другой — водителей, механики большинства предприятий фактически постоянно тушат возникающие «пожары». Такой тип построения работы в России считается обычной практикой. Он повышает значимость механиков и оказывает существенное влияние на формирование рынка. Для практикующего механика специалист, который не «тушит пожары», — теоретик, и относятся к нему с некоторым пренебрежением и даже иногда с высокомерием. На такую практику любят опираться государственные органы.
Технические требования
Часто вначале общения получаешь сокращенное описание прицепа какой-то марки: «Сделайте, пожалуйста, точно такой же, с минимальными изменениями, если необходимо. Главное — цена!».
На такие запросы с годами сложился заготовленный ответ: «Извините, но в ваших требованиях описаны технические характеристики модели одного из производителей. У них свое видение, у нас — свое. Чтобы наше решение было эффективным, необходима постановка транспортной задачи. Модель прицепа коллег мы не производим».
Когда я посмотрел первоначальные технические требования в этой истории, у меня немного отлегло от сердца. В контакте — профессионал. Редко характеристикам средств фиксации груза изначально уделяют внимание: «За основу берем полуприцеп модели Jumbo (фото 1) с самым низким расположением задней части, снимаем надстройку и оставляем голую платформу. Вместо 23 пар скоб для крепления стяжных ремней с нагрузкой 2500 daN устанавливаем 10–12 пар колец с нагрузкой 5000 daN . Уточните, пожалуйста, допустимую удельную нагрузку на нижнюю часть в базовой комплектации».
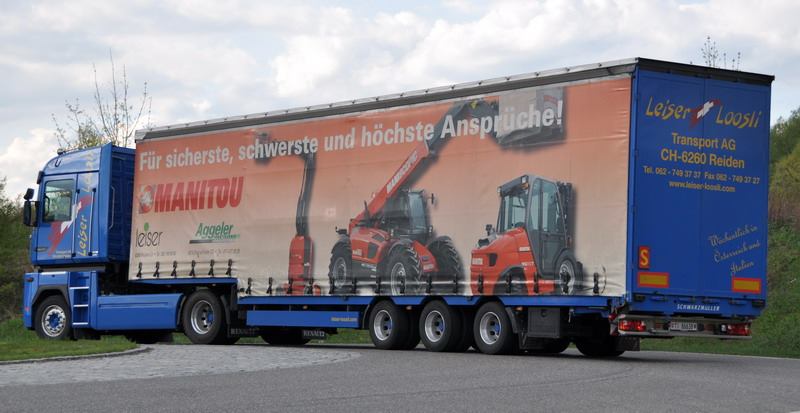
Фото 1. Автопоезд с полуприцепом Jumbo (Harm Adams)
Прицеповедение
Главная деталь полуприцепа — рама. Она состоит из двух продольных лонжеронов переменной высоты, выполненных, как правило, в форме двутавра, и поперечных соединительных балок – траверс, которые по периметру опоясывает внешняя рамка. С начала XXI века идет активный процесс оптимизации веса полуприцепов, поэтому конструкция рамы и в целом полуприцепа одного типа в зависимости от допустимой нагрузки может сильно меняться.
Особенность модели Jumbo — наличие двух грузовых платформ: верхней и нижней. Ценность представляют характеристики второй. Она располагается на высоте около 0,9 м от земли и позволяет перевозить грузы высотой примерно 3,1 м, оставаясь в допустимом верхнем габарите 4,0 м.
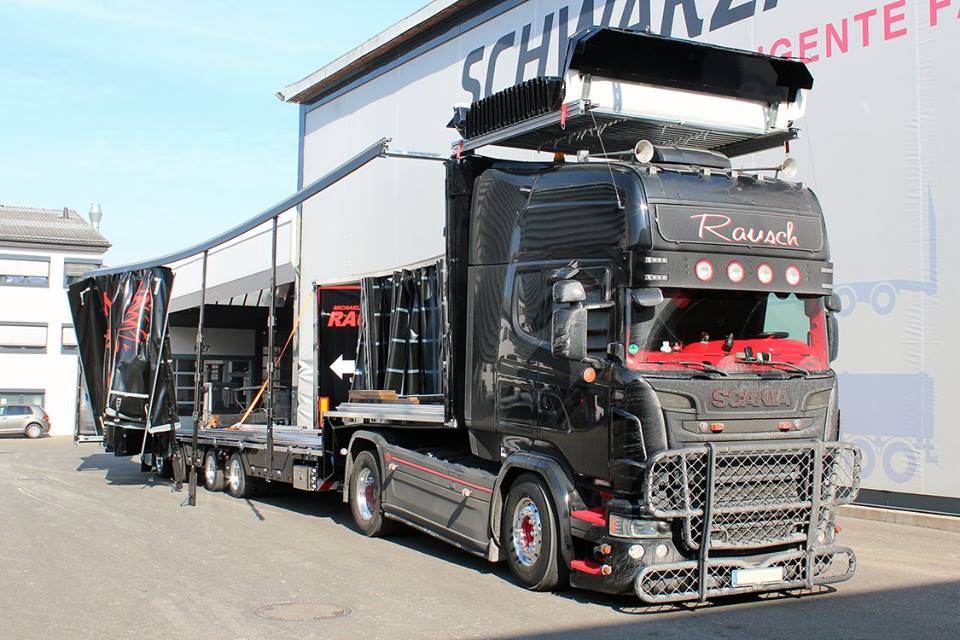
Фото 2. Для удобства погрузки механизм крыши полностью сдвигается в положение над кабиной тягача. В полу предусмотрены ниши для перевозки колесного транспорта (Schwarzmüller)
На любой полуприцеп воздействуют два основных типа нагрузок. Один из них — продольный прогиб рамы под тяжестью груза. При неудачной конструкции или перегрузе полуприцеп может «сложиться». За предотвращение этого разрушительного воздействия отвечает конструкция лонжеронов.
Второй тип — кручение рамы вокруг продольной оси из-за неровностей дороги. На его минимизацию направлена конструкция траверс и внешней рамки. Сложность конструкции Jumbo в том, что рама — как рукоятка кривого стартера, забытого уже инструмента для ручного запуска двигателя автомобиля, имеет изгиб и особенно требовательна к перечисленным типам нагрузок.
Jumbo используется в основном для перевозки станков, оборудования и специализированного транспорта. Европейские перевозчики предпочитают комплектации со сложной надстройкой, где для погрузки водителем раздвигаются или поднимаются все элементы за 10–15 мин (фото 2 и 3). В полуприцепе закрытого типа ниже риск испортить груз при транспортировке. В России и Америке выбирают более примитивный и дешевый вариант открытых платформ.
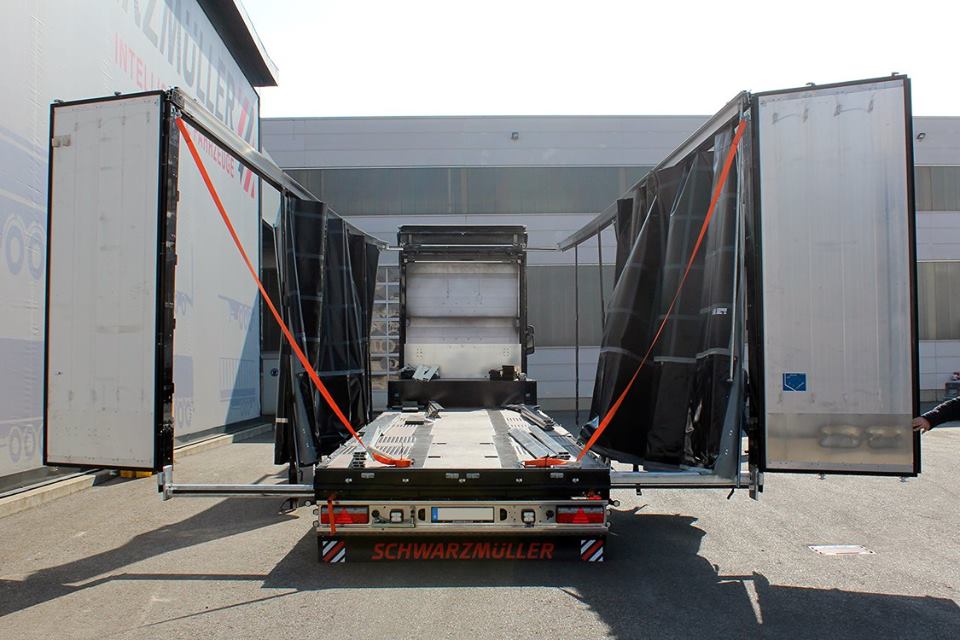
Фото 3. Для погрузки и перевозки негабарита надстройка полуприцепа раздвигается в стороны на ширину 4,0–4,5 м по всей длине (Schwarzmüller)
Работа с механиком
Желание установить усиленные кольца для крепления груза вызвало вопросы о нагрузке. От нее зависело устройство полуприцепа и изменение его стоимости.
Пока мы ждали расчета и решения из Австрии, обсуждали возможность установки крепежных колец, рассчитанных на 5000 daN (фото 4) в стандартную внешнюю рамку и необходимость усиления траверс. Мне казалось, достаточно просто понять элементарную логику: кольца с увеличенными характеристиками требуют усиленной конструкции внешней рамки и «проводников» передающей нагрузки на лонжероны, которыми являются траверсы. В базовом варианте они не рассчитаны на дополнительную нагрузку.
Фото 4. Типы скоб и колец с разными техническими характеристиками для крепления груза (Тарас Коваль)
Но механика смущали фотографии скоб и рамок других производителей. Локальное увеличение параметров отдельных элементов свойственно прицепостроителям, не специализирующимся на сложном подвижном составе, и используется по просьбе клиента, если оно ему согревает душу. Например, на осевой агрегат с нагрузкой 10–11 т устанавливаются 9-тонные колеса.
Для поиска взаимопонимания с механиком пришлось обратиться к директору компании. На мое счастье, это женщина. Задал ей вопрос: что будет с ее кроссовером, если к рейлингам на крыше закрепить палету с двумя 200-килограммовыми бочками масла? Не знаю, какие слова находит женщина-руководитель в подобной ситуации, но больше это решение с механиком не обсуждалось. С директором-мужчиной в подобной ситуации обычно сложнее.
Получив описание основных грузов, мы увидели значительный объем негабаритных грузов по ширине. Возникло предложение установить кольца, которые для удобства работы с такими грузами могут в горизонтальном положении выходить за ширину прицепа, упрощая процесс крепления (фото 5).
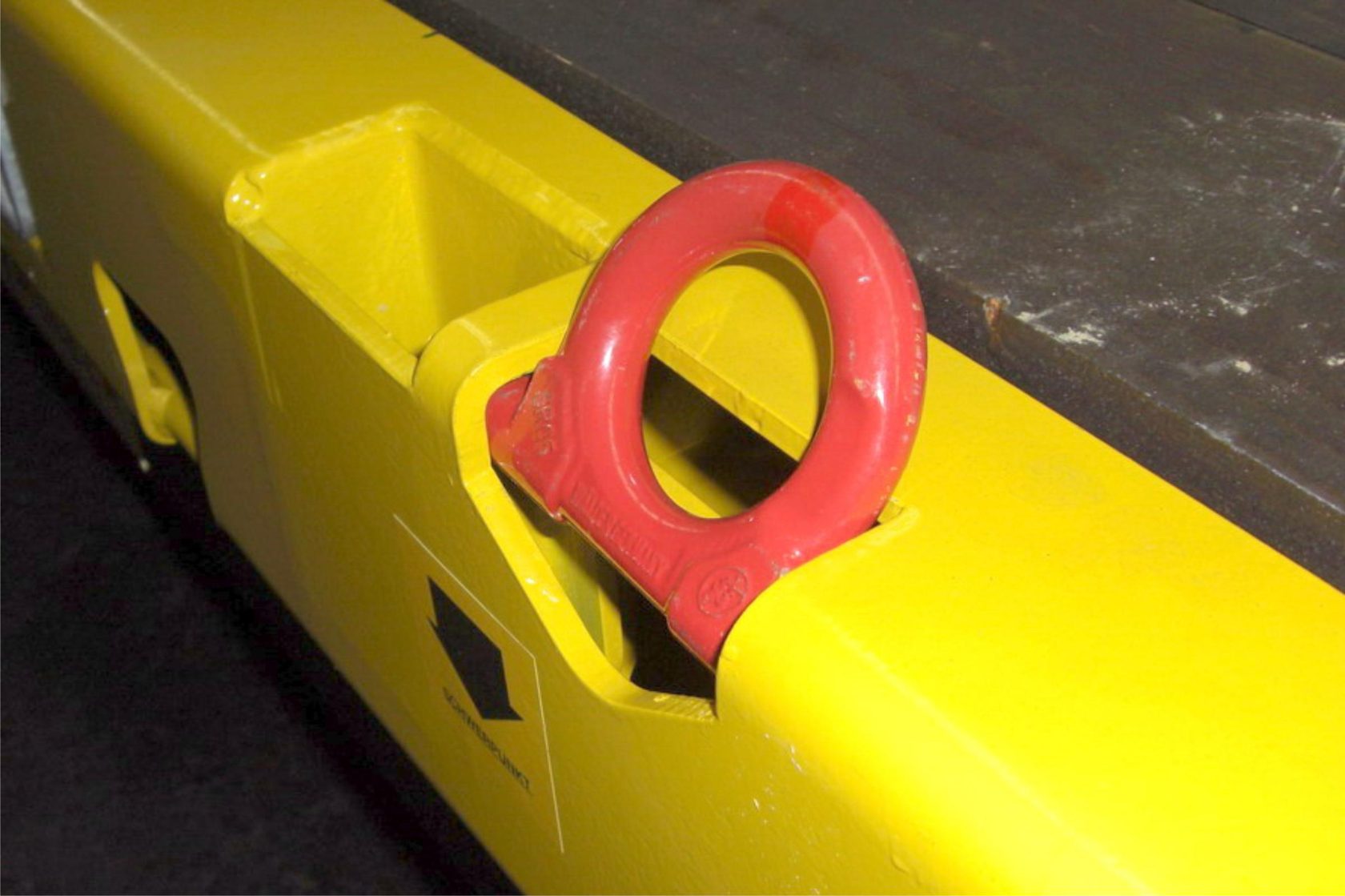
Фото 5. Специальное кольцо крепления груза, работающее как в вертикальном, так и горизонтальном положении (Schwarzmüller)
Чем ниже расположена задняя платформа, тем больше возможностей перевезти более высокий груз, оставаясь в пределах допустимых ограничений. Исполнение упирается в диаметр колеса и колесную арку, которая может выступать над уровнем пола. Но чем ниже колесо, тем меньше допустимая на него нагрузка. При использовании колес размерностью 235/75R17,5 погрузочная высота — 920 мм, техническая нагрузка на три осевых агрегата — 27,0 т. Меняя размер колеса на 215/75R17,5, получаем 880 мм и нагрузку только 24,5 т. В гамме продукции Continental есть специальные шины 205/75R17,5, которые позволяют снизить погрузочную высоту до 820 мм, минимально уменьшив нагрузку до 24,0 т.
Но возникла другая проблема. Для крепления корзины запасного колеса тягача размерностью 315/70R22,5 было место только снизу полуприцепа. В первом варианте остается всего 170 мм дорожного просвета, в последнем — 100 мм. Также чем больший кривошип образует геометрия полуприцепа в месте перехода от «балкона» к нижней платформе, тем большее усиление необходимо. При выборе компромисса между высотой задней части, удельной нагрузкой и стоимостью полуприцепа остановились на базовых для этой модели колесах 235/75R17,5.
Из-за повышенной удельной нагрузки 23 т на 4000 мм в центе тяжести полуприцепа и наличия в задней части U-профиля крепления механических рамп для заезда специальной техники длину нижней платформы пришлось сократить. В результате «балкон» остался 4000 мм с погрузочной высотой 1300 мм, а длина платформы уменьшилась до 9500 мм с погрузочной высотой 920 мм. 12 пар крепежных колец нагрузкой 5 т утопили в наружной части рамки.
Пришла пора цеплять тягач.
«Сообразим на троих»
Для любого полуприцепа важны геометрические параметры седельного тягача. Для предложенного нами варианта они практически стандартные:
- 2-осный с пневматической подвеской
- Сцепная высота в порожнем состоянии 1140 мм
- Без дополнительных надстроек
- Максимальное расстояние от передней точки седельного тягача до сцепного шкворня — 4500 мм
- Минимальное свободное расстояние перед сцепным шкворнем (передний радиус ометания) — 2240 мм
- Максимальный радиус от сцепного шкворня до задней крайней точки (задний радиус ометания) — 1900 мм
Но неожиданно выяснилось, что автопроизводитель имеет свой взгляд на седельный тягач для этого проекта. Перевозчику был предложен автомобиль с колесной базой 3900 мм, двумя топливными баками по бокам, занимающими почти всю длину между мостами и аккумуляторным отсеком в задней части рамы.
При такой комплектации ведущий мост как бы отодвигается от седельно-сцепного устройства и часть нагрузки с него перемещается на рулевую ось. Такая геометрия снижает риски штрафов из-за перегрузов ведущей оси, нормативы по которым установлены в России еще во второй половине XX века, а также появляется возможность заправляться топливом в удобном месте. При существенной разнице цен на него в странах Европы это очень актуально.
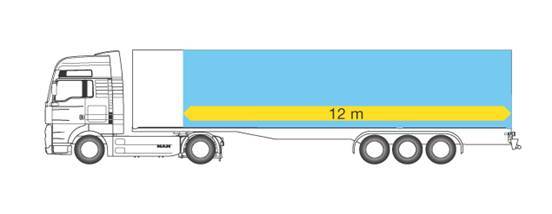
Рис. 6. Европейское ограничение для седельных автопоездов: 12 м от сцепного шкворня полуприцепа до крайней задней точки (Rollerreiner)
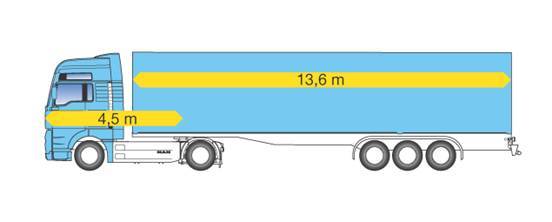
Рис. 7. Европейское ограничение для седельных автопоездов: 4,5 м от переднего габарита тягача до оси седельно-сцепного устройства (Rollerreiner)
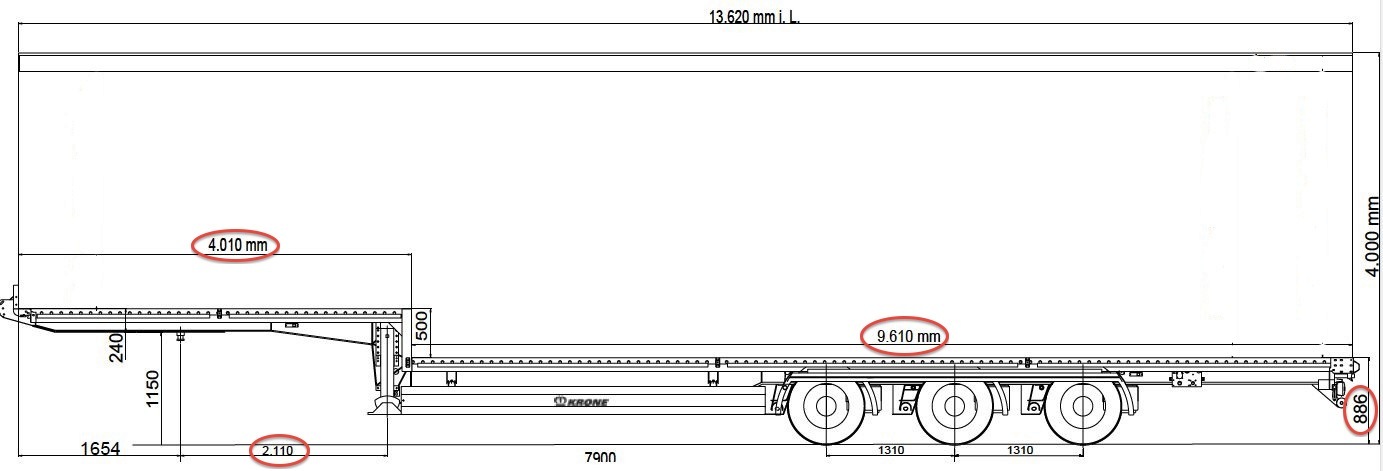
Рис. 8. Основные габаритные размеры полуприцепа Krone модели Jumbo в базовой комплектации (Krone)
Сравнивая два чертежа, я заметил: «У нас в базе даже 9620 мм (рис. 9). Но при такой конфигурации тягача радиус заднего ометания 2280 мм, а у коллег на схеме расстояние только от центра сцепного шкворня до оси опорных лап 2110 мм».
Механик спросил: «Говорить с автопроизводителем, чтобы двигали седло? Сколько будет расчетная длина автопоезда в случае превышения на 11см? Сколько составят «балкон» и «платформа»?»
Я ответил: «Если двигать седло назад, то преимущество остается только в объеме топливных баков. Нагрузка на ведущую ось увеличивается почти до размеров автомобиля со стандартной базой, и постоянно на территории Европы будет необходимо разрешение на негабарит».
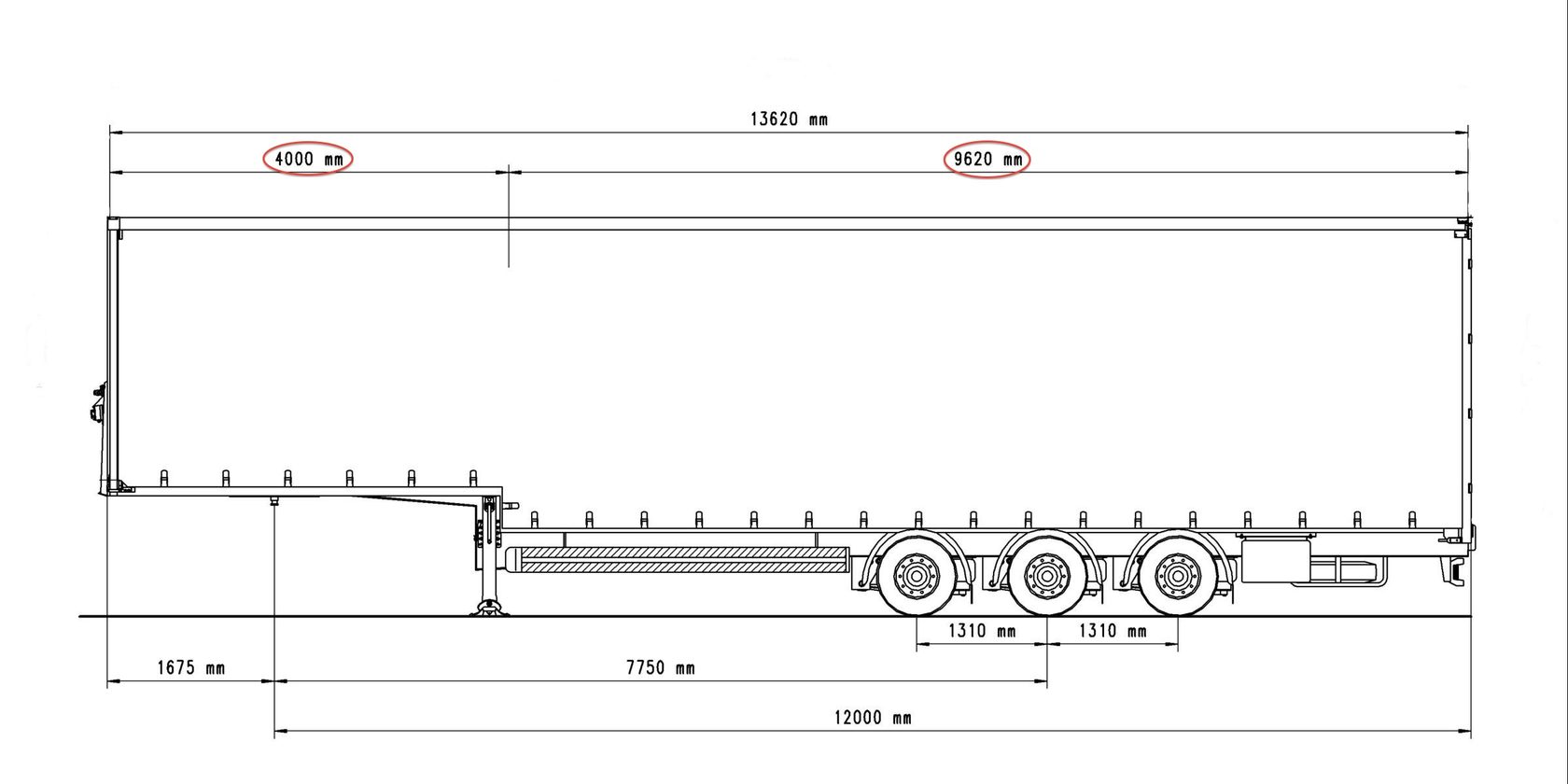
Рис. 9. Основные габаритные размеры полуприцепа Schwarzmüller модели Jumbo в базовой комплектации (Schwarzmüller)
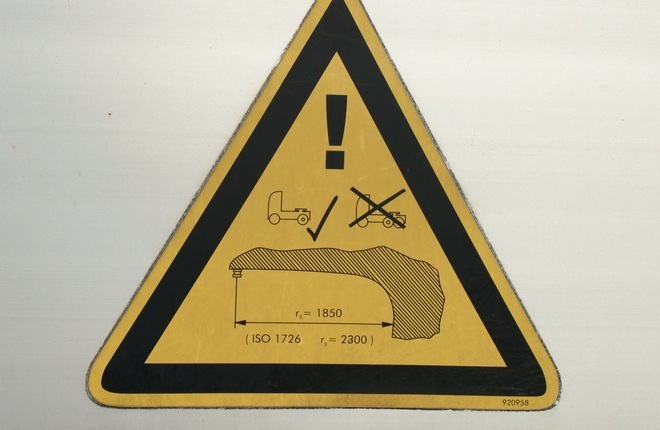
Фото 10. Предупреждение на передней стенке о сцепных характеристиках полуприцепа Schmitz (Тарас Коваль)
«Но как? — подумал я. — Геометрия — она либо есть, либо ее нет. С ней нельзя договориться». Звоню механику: «Давайте определимся, что для вас важнее: большие баки и уменьшение рисков перегруза ведущей оси или длина платформы?»
Иногда мнение о человеке меняется мгновенно. Последовавший ответ механика оставил позади предыдущие споры и некоторое недоверие к нему: «Во главу угла нашего бизнеса поставлена продажа провозных возможностей платформы, а не экономия топлива, хотя она тоже важна, поэтому меняем конфигурацию тягача». Я зауважал его искренне, как профессионала с большой буквы.
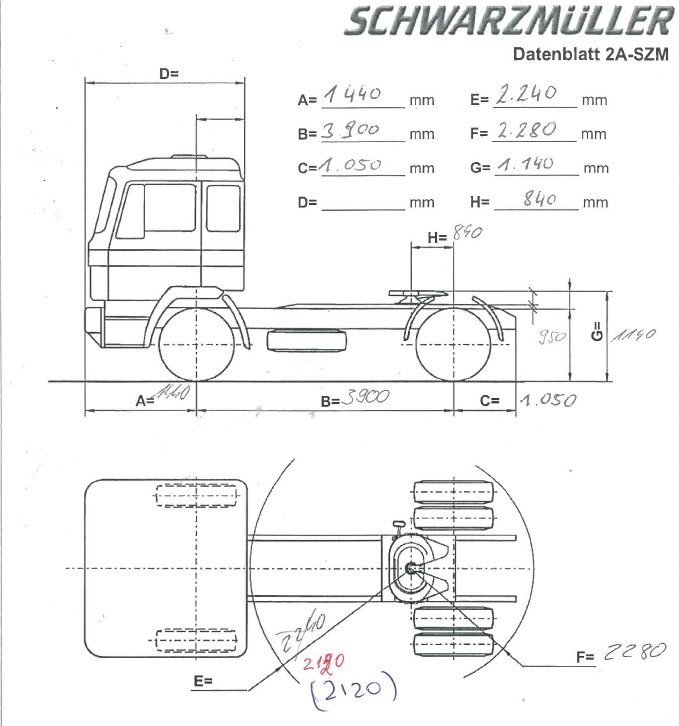
Рис. 11: Основные геометрические параметры предложенного седельного тягача с колесной базой 3900 мм (Schwarzmüller)
Вторая попытка: база 3600 мм
Автопроизводитель прислал чертеж тягача с колесной базой 3600 мм. Австрийцы почти сразу попросили утвердить новый чертеж-рисунок. Но неожиданно подоспела новая порция упражнений в технической смекалке.
От автоизготовителя приходит письмо, где задний радиус ометания больше, чем нужен, а передний — наоборот, меньше (рис. 12). С такими данными полуприцеп позади седла будет царапать заднюю часть тягача и опорные стойки полуприцепа, а спереди — сносить кабину или элементы надстройки за ней.
Лезу в фотоархив, где нахожу автопоезд в нужной комплектации на домашней выставке Schwarzmüller в 2012 году. Отправляю автопроизводителю.
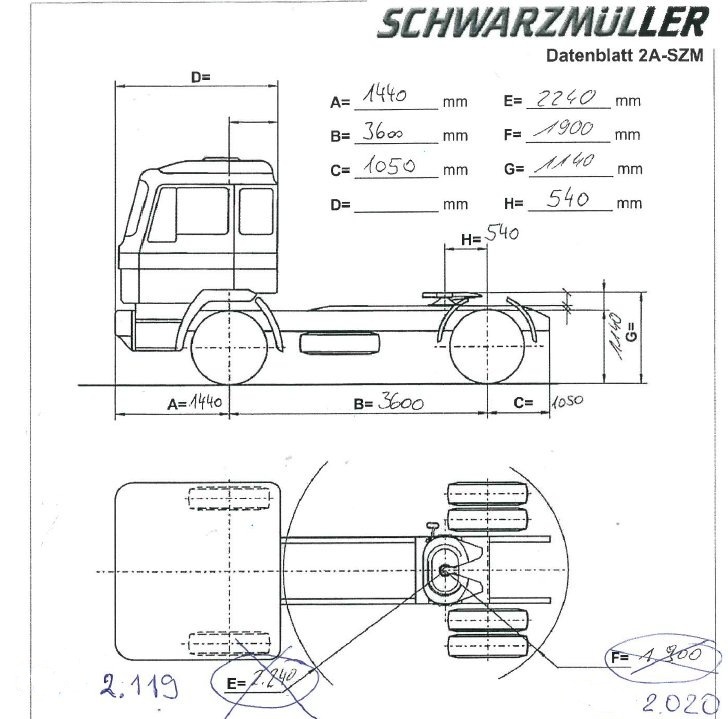
Рис. 12: Основные геометрические параметры предложенного седельного тягача с колесной базой 3600 мм (Schwarzmüller)
Далее автопроизводитель спрашивает: «А как ваши считают задний радиус ометания? Мы — по теореме Пифагора. Одна сторона треугольника чуть меньше половины габаритной ширины. Вторая — сумма расстояний от центра седла до центра ведущей оси и от нее до задней точки рамы. Соответственно, искомое нам расстояние — гипотенуза треугольника — равно квадратному корню из суммы квадратов других сторон».
Логично и просто. Учите математику. Пригодится в неожиданном месте.
Прежде чем отправить учебный вопрос по автоделу в Австрию, сам пересчитываю и проверяю. Разворачиваю чертеж тягача во весь монитор офисного компьютера и по-быстрому прикладываю к нему линейку (рис. 13).
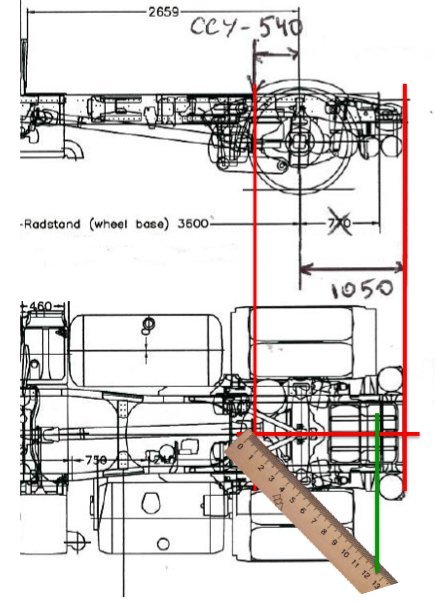
Рис. 13 : Быстрый приблизительный расчет при помощи линейки радиуса заднего ометания (коллаж: Тарас Коваль)
Действительно, предложенный расчет был бы верным, если бы дальняя точка была окончанием рамы. Но миллиметры на линейке показывают, что интересующая нас крайняя точка — угол заднего габаритного фонаря, проекция которого расположена ближе к ведущей оси тягача, чем крайняя точка рамы с аккумуляторным отсеком. Радиус ометания получается примерно 1810 мм. До максимальных 1900 мм есть еще запас. С чувством выполненного долга и надеждой, что с передним радиусом автопроизводитель справится без меня, отправляю письмо с расчетами.
После собрания технических специалистов мне приходит ответ: «С задним вопрос решили, извини. Теперь с передним проблемы. Надо 2240 мм, а есть только 2119 мм».
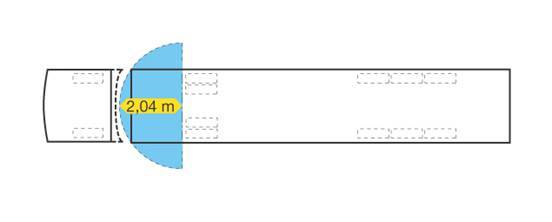
Рис. 14. Максимальный радиус переднего «угла» полуприцепа (Rollerreiner)
Приходит ответ, что по корпоративным нормам этого делать нельзя. Я отвечаю: «Тогда у нас есть два варианта продолжения: 1) вы находите техническое решение, удовлетворяющее нашим требованиям, или 2) берете ответственность на себя, подписываете наши требования по геометрии и переходим к производству полуприцепов. До решения вопроса мы вынуждены приостановить проект».
Пишу письмо, а самого гложут сомнения: может, мы и вправду перестарались с требованиями? Этот перевозчик эксплуатирует еще одну марку автомобилей. Связываюсь с их технической службой. Получив в ответ чертеж нужного тягача, понял, что все корректно. В личном рейтинге второй производитель укрепляется на позиции первого номера в России. Отправляю копию ответа механику.
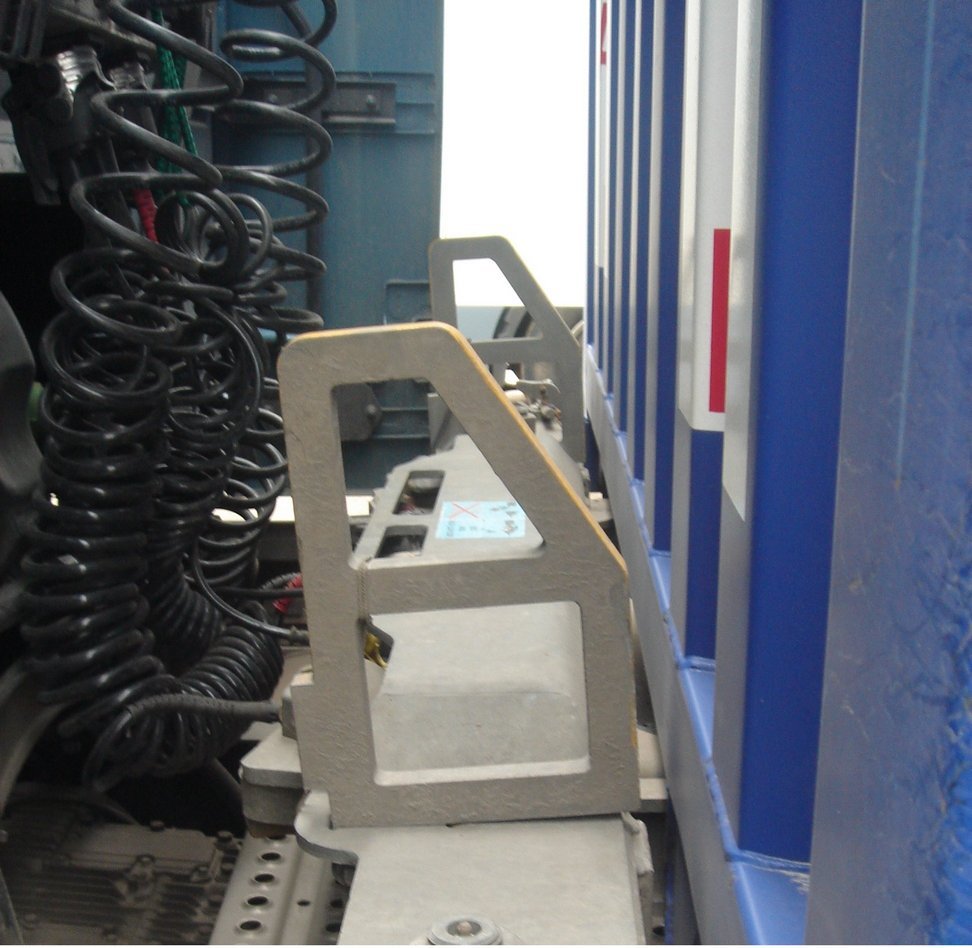
Фото 15. Спиралеобразные соединительные шланги и кабели между тягачом и полуприцепом при перевозке 45-футового контейнера в европейском габарите автопоезда в 16,5 м (Тарас Коваль)
Логистика
В начале марта президент России Владимир Путин выступил на заседании Союза транспортников. В своем выступлении он акцентировал внимание на неравных условиях отечественных транспортных компаний по сравнению с иностранными конкурентами и поручил правительству совместно с объединениями автоперевозчиков проанализировать эту ситуацию.
На протяжении почти двух десятилетий идет поиск решений для равной конкуренции международников. Перевозчики упрямо предлагают два механизма: локальные льготы им и методы административных запретов. Несмотря на очень низкую эффективность такого подхода, упорная борьба и выдвижение новых идей в этом направлении продолжаются.
Приоритет развития транспорта для увеличения объемов международной торговли подталкивает к принятию международных стандартов. С 1899 года мы используем метрическую систему мер, и нас не смущают ее французские корни.
В автотранспорте не сложилось единой мировой системы стандартов. Но большинство требований по сертификации, весогабаритным параметрам, рабочему времени и др. опираются на регулы Европейской экономической комиссии ООН и директивы Европейского союза. Непонимание и неприятие европейских инструментов мешают использовать внутри страны хорошо зарекомендовавшие себя стандарты и технологии, а также привязанный к ним интерес инвестирования в автотранспорт. Наверное, можно придумать свои. Только есть ли логистический смысл делать «разную по ширине колею» еще и в автотранспорте? Без кардинального решения этого системного вопроса мы так и будем топтаться на месте с упорством, достойным иного применения, и продолжать «наступать на швабру».
С вступлением в эпоху цифровизации недоработки в алгоритме построения задачи для автотранспорта на государственном уровне приводят к проблемам в работе всей логистики, мешают развитию автомобильной промышленности и экономики в целом. Но пока попытки решения локальных проблем остаются главной тенденцией российского автотранспорта.